All service organizations have one thing in common: They want to carry out repair orders and maintenance work in an efficient and service-oriented manner. In the past, field service was responsive, and the service provider depended on visits by its technicians to customer facilities to identify faults, or via calls from customers when the end units went bad. This wasted time, resources and money. Today, in the digital age, field service is proactive and end units are becoming smarter, IoT-based, creating an intelligent edge and reporting their status. The service provider decides what to do according to these reports. It is no longer necessary to wait for the customer to report that the end unit is not working or that maintenance is required.
Making the old-style responsive field service a proactive one
Cloud of Things, a Prodware partner, helps make traditional responsive field service proactive with their DeviceTone Genie product. It transforms products with smart devices and bridges the gap between the product and the cloud, making the device IoT-ready within minutes.
For example, Cloud of Things serves a company that provides water bars. Each bar has a 5-gallon bottle that must be replaced when it is about empty. A DeviceTone Genie-enabled IoT device, installed beneath the water bar, weighs the bottle and sends an alert to the service provider when the bottle is nearly empty. The alert is received in the service provider’s Microsoft Dynamics 365 Field Service system that automatically generates a new order for a 5-gallon bottle (or bottles – depending on the client’s number of water bars) to be sent to the customer’s home or office.
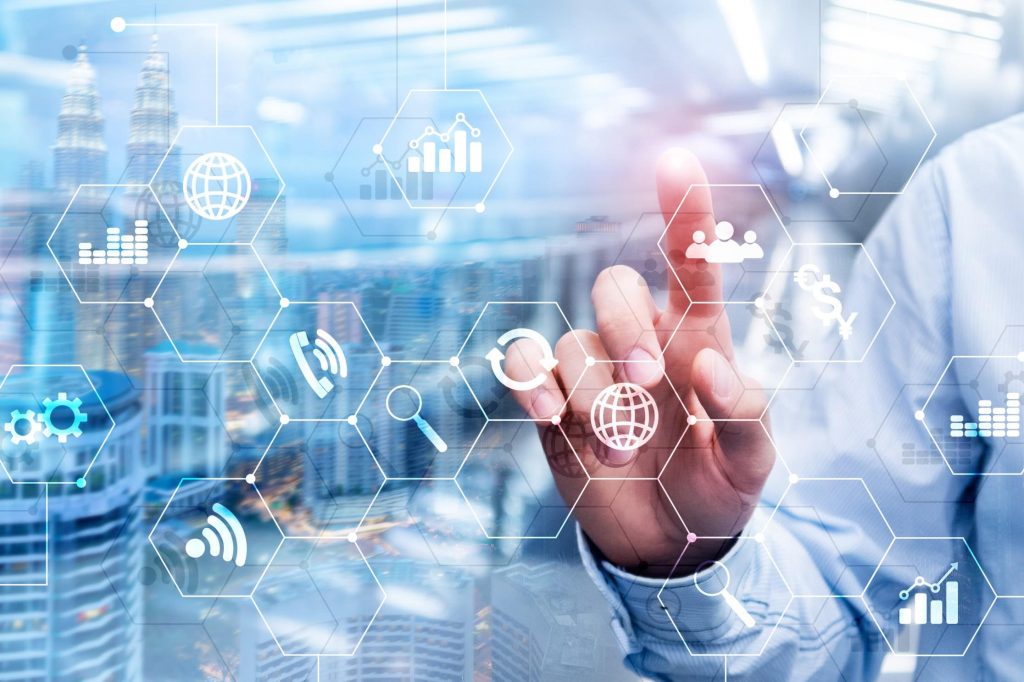
This is a good illustration of field service becoming proactive, which greatly improves the customer journey. It saves time and resources for the customer, as well as for the supplier. There is no need to check the water level in the field, to send unneeded water bottles to customers or to send them a replacement late, after the 5-gallon bottle is already empty.
Another example is connecting a pizza oven running DeviceTone Genie to Microsoft Azure IoT. The ovens need to maintain a certain temperature. If the oven cannot reach the required heat, the pizza is not tasty; affecting the hospitality owner’s reputation. The IoT-enabled device inside the ovens reports the oven’s temperature to the field service. If the oven temperature is lower than required, a technician is sent to fix it. In the past, the pizza shop could detect the problem only by complaints from customers.
These are examples of how digitization improves field service and the operational efficiency of the systems that operate and maintain end units. In fact, it is not just the end units but the whole chain that handles the process, from the order to the supply and maintenance of the purchased end units.
Automatic optimization of technicians’ driving routes
The modern field service management system also includes automatic optimization of the technicians’ driving routes. It knows how to optimize the route of a technician who must visit several places during the day, taking into consideration the traffic load, the location of customers, and the urgency of customer calls. The system also knows how to make vehicle allocations to technicians and suitable equipment that the technician must take on the same day to the field, depending on the types of calls. For example, Microsoft Dynamics 365 Field Service allows dispatchers to view a technician’s daily turn-by-turn routes to easily add nearby appointments, minimize driving time and understand upcoming traffic constraints.
Microsoft Dynamics 365 Field Service offers many possibilities in the service and maintenance environment with the integration of mixed-reality technologies. Whether virtual, mixed or augmented reality – the diversity of these technologies allows organizations to be more productive and accurate in their service provision – from training through to on-site resolutions.
Using mixed reality as an integrated field service tool
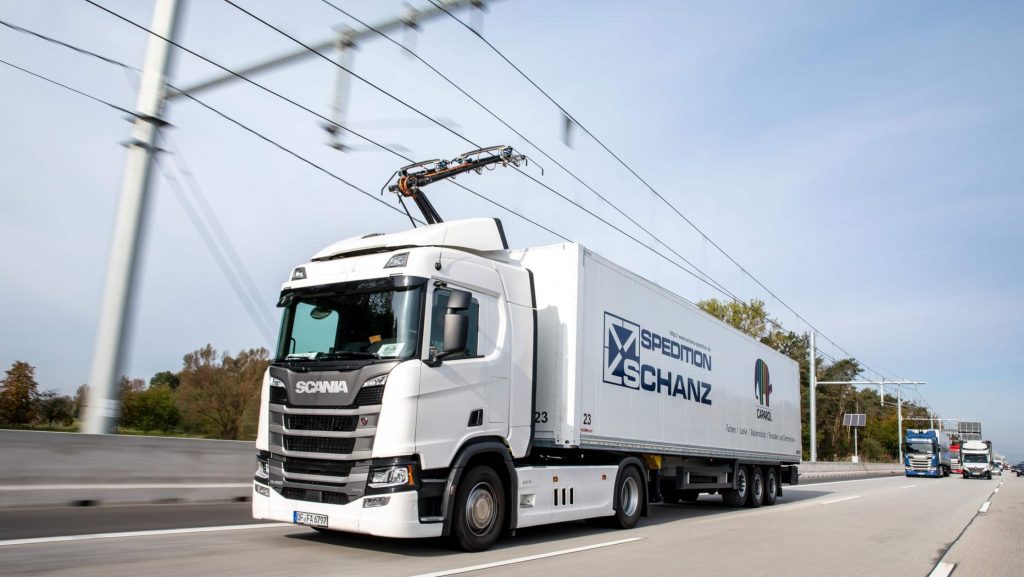
Prodware supported its partner Siemens in a project called “eHighway.” In this Proof of Concept project, Siemens revolutionizes freight transport on roads. Similar to electric trains, the eHighway truck connects with a pantograph to an overhead contact line and can still drive large distances, independently from its heavy freight. It is a fully electric, very safe, efficient and especially ecological solution. During the commissioning before the e-hybrid truck operates for the first time, a technician checks the flawless operation of the pantograph with a Microsoft HoloLens head-mounted AR display. The technician uses Augmented Reality to provide all relevant information; to prepare better for actual usage. The digital model allows components to be viewed in detail. Safety is also improved by information videos that warn engineers about hazards. The service employee has full access to documents and information, and a service screen displays the measures to be implemented.
This scenario demonstrates the importance of digital remote assistance in the digital age. Microsoft Remote Assist’s real-time data transfer simplifies collaboration over large distances. The engineer and the head office see what the technician on site sees. At the end of the work the engineer evaluates the job. Using the HoloLens, the technician can also record what he is doing, as well as see important information projected through the glasses, such as the call details. This way, the technician’s hands are free, and he does not need to hold pages, a computer or a telephone, which in the past would have complicated the work and made it difficult for the technician.
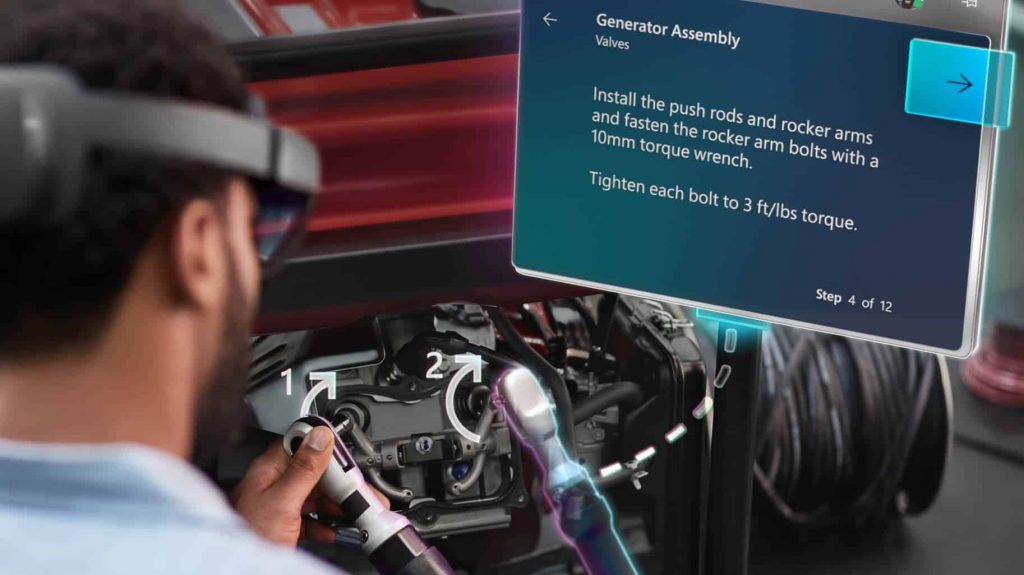
The use of Microsoft Guides with HoloLens supports technician onboarding and ongoing training to ensure best practice and faster ROI of overheads in field service provision. Ditch the training manuals and provide workers with step-by-step guides on their devices with holographic parts icons that can be picked up, supported by HoloLens so they can see in real-time and real-life the right process to follow.
An innovative field service management solution
Microsoft Dynamics 365 Field Service delivers intelligent and connected maintenance technologies, including scheduling, customer assets, work order management, product inventory, billing, mobility and resource optimization.
Companies can move from a costly break-fix model to a proactive and predictive service model.
Using this leading field service app as our central platform, Prodware injects additional innovation such as IoT with the DeviceTone Genie and also with AI, helping technicians on-site with our Spare Part Finder mobile app.
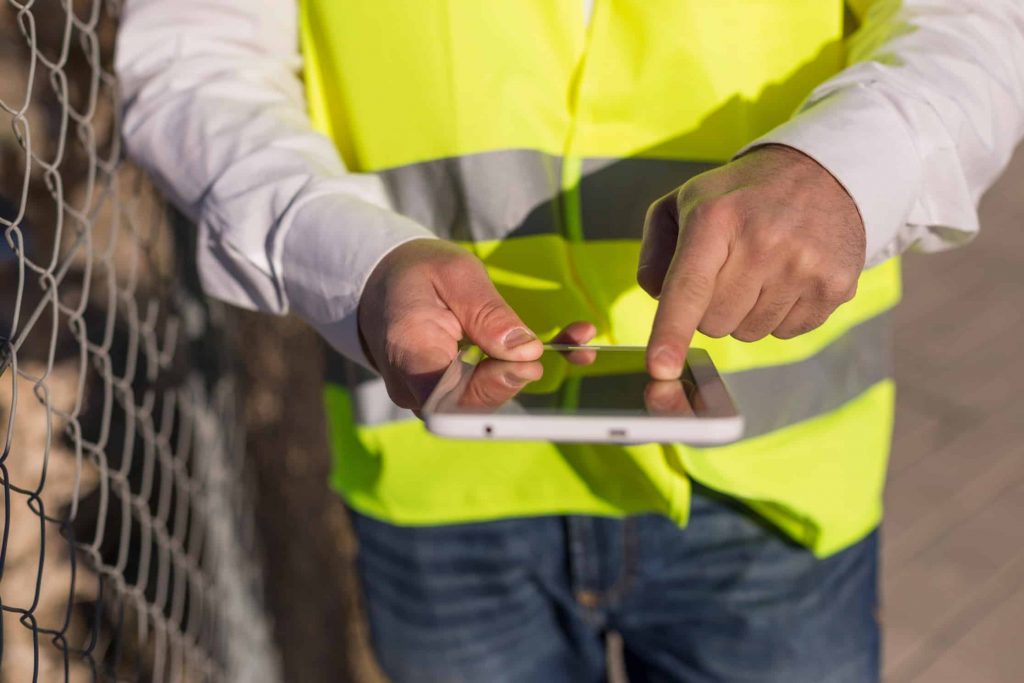
Integrated with Dynamics 365, the app resolves issues technicians encounter when they need to locate a spare part in order to complete a repair on-site. The technician simply points the app’s camera at the part to replace and using AI Custom Vision, it automatically captures images and recognizes the product and its ID reference to allow for timely retrieval of the part (whether it’s in the van or back in stock or needs to be re-ordered) to speed up resolutions, work order updates and provides transparency to the customer.
With the inclusion of IoT and AI machine learning capabilities In Prodware’s field service offering; customer experience is truly be placed at the heart of your business.
As a trusted business innovation adviser, Prodware is instrumental in driving customers’ field service into the digital age. Ask me about our consulting services to get you on the right track for your own successful digital transformation of field service.